Как снять лампочку ближнего света на Фольксваген Поло седан видео
Поездка в Калугу, Часть 2: Завод Volkswagen
Продолжение репортажа о путешествии в Калугу на завод Volkswagen.
По замыслу организаторов, журналисты стартовали от дверей салона Фольксваген Центр Внуково в 9 часов утра и должны были прибыть к центральным воротам завода не позднее 11.30. По дороге колонна не держалась друг друга: некоторые ехали медленно и снимали внешний облик немецкой новинки, другие раскочегаривали машину до упора. На всем протяжении маршрута висят солидного размера указатели, поэтому промахнуться и не доехать до места назначения практически невозможно.
Немцы, следуя поговорке «Голодное брюхо к учению глухо», организовали потрясающего вида фуршет, но из-за сорокаградусной жары наибольшим спросом пользовались напитки, выпитые к моменту выступления руководства подчистую.
По правилам российского законодательства, иностранное производство имеет право три года производить автомобили по технологии крупноузловой сборки, за рубежом именуемой Semi-Knocked Down. На без пяти минут собранную машину в Калуге устанавливался двигатель, детали салона и некоторые агрегаты. По прошествии трех лет производитель обязан перейти на мелкоузловую сборку (Completely Knocked Down), инициализируя тем самым все цеха производства, включая штамповку, сварку разнообразных деталей, окраску и конечную сборку.
На данный момент четыре машины концерна VAG полностью собираются на территории калужского завода. Это Skoda Octavia FL, Skoda Fabia, Volkswagen Tiguan и, недавно поставленный на конвейерную линию, Volkswagen Polo седан. Стоит заметить, что в октябре нынешнего года Octavia Tour окончательно сойдет с конвейера и на калужском предприятии эта модель не представлена ни в кузове хэтчбек, ни в кузове универсал (Combi). Fabia собирается только в кузове хэтчбэк.
Первый цех, в который мы прибыли, гордо встречает сотрудников эмблемой Gestamp Severstal Kaluga. Альянс российского и испанского производителей будет выпускать порядка 13 миллионов штампованных деталей в год. Другое производство, именуемое «Северсталь-Гонварри-Калуга», занимается выпуском металлопроката с мощностью 170 000 тонн в год, лишь 70 000 из которых пойдет на автомобильную промышленность.
Как рассказал испанский представитель «Гестампа», Volkswagen на данный момент не удовлетворен качеством российского металла и вынужден сотрудничать с прежним поставщиком, компанией ArcelorMittal. В будущем немецкий производитель планирует перейти на российскую штамповку, как это сделали в французском предприятии «Автофрамос». К слову, на Polo ставится отечественная резина KAMA и российские стекла.
Итак, готовые листы доставляются в цех уже будучи обработанные цинком. Это важный момент, поскольку оцинкованный с обеих сторон кузов не поддается коррозии. Благодаря подобному технологическому процессу, Volkswagen дает гарантию 12 лет от сквозной ржавчины. Более того, я лично знаю владельца Шкоды 2000 года выпуска, сколы на которой не цветут и по сей день.
Представитель компании охотно разговаривает на русском языке с чуть уловимым испанским акцентом. Рядовые сотрудники производства, в отличие от управляющих менеджеров, по-русски не разговаривают и отвечают жестами «Тише» на вопросы журналистов. На заводе работают российские работники, за исключением как раз-таки штамповочного цеха.
В штамповочном цеху располагаются три конвейерные линии с запасом места для расширения мощности до четырех. Проектная мощность завода составляет 150 тысяч автомобилей в год и, учитывая 24 модели Audi, Skoda и VW, собираемые по технологии крупноузловой сборки, совсем скоро дополнительная поточная линия может быть развернута. Автоматизированные роботы штампуют 133 разнообразных деталей.
Естественный для данного этапа процесс это контроль за деталями, выходящими с конвейерной линии.
В соседней комнате работают испанские сотрудники «Гестампа», занимающиеся выявлением и анализом огрехов в производстве.
Люди преданы своей стране даже в России :)
За цехом штамповки находится склад, куда поступают готовые детали.
По длинному коридору, больше похожему на водонепроницаемый ангар, мы попадаем в сварочный цех (VGR Karosseriebau), где нас встречает уже российский специалист.
Сварочный цех структурирован. Один поток отвечает за VW Tiguan под проектным номером VW316 RU. Следующий поток предназначен для Skoda Octavia (SK351). Третий поток разделил между собой VW Polo (VW251) и Skoda Fabia (SK250).
Каждый отдельный участок отвечает за конкретную кузовную часть и имеет порядковый номер. Сваркой малогабаритных деталей занимается сотрудник со сварочными щипцами.
Крупные части кузова сваривает робот. Точки сварки в виде координат заложены в электронную программу, что сводит на нет ошибки в процедуре.
На всем производстве установлены датчики, которые останавливают работу робота, лишь стоит человеку попасть в зону их действия.
Многие покупатели, услышав от друга, который знает товарища, который говорил с приятелем о посредственном качестве российской сборки, не желают покупать машины местного производства. Понимаете, производитель, вкладывающий миллионы долларов инвестиций в строительство предприятия и обучение местного населения, не станет экономить минимальные средства на контроле качества. Для набора сотрудников концерн сотрудничает с тремя профильными кадровыми агентствами, отбирающими требуемый персонал. На каждой из финальных стадий производства, помимо датчиков, следящих вплоть за усилием вкручиваемого болта, представители Volkswagen производят осмотр продукции. По словам начальника цеха, проходившего обучение в Германии, на российском производстве аудит ведется с удвоенной тщательностью.
Покрасочный цех, в силу технологических причин, скрыт от прямых глаз прессы. Нас можно было одеть в специальные костюмы, но из-за ограниченности по времени процесс был показан по телевизору. Готовый кузов грунтуется путем погрузки в специальную ванну и красится несколькими слоями. После каждого из этапов конструкция отправляется на сушку в специализированную печь. Производственная мощность покрасочного цеха включает в себя 16 вариаций цветов, совпадают из которых лишь серебристый на Октавии и Тигуане. Более широкая гамма цветов кузова требует промывки роботов, что финансового нецелесообразно.
От момента появления кузова машины до полной покраски поточной линии требуется 6 часов. По словам начальника цеха, каждые две минуты на сборочный конвейер выходит покрашенный автомобиль.
Немного цифр о монтажном цехе мелкоузловой сборки. Занимаемая с учетом так называемого «Супермаркета» площадь равняется 50 000 квадратных метров. Supermarkt немцы называют площадку с контейнерами разнообразных деталей, устанавливаемые на этапе сборки автомобиля. 26 тысяч квадратов занимает сам цех, еще 24 000 отведено под запчасти. Проектная мощность подразделения — 31 автомобиль в час. На данный момент завод работает в одну смену, но функционально может трудиться в три.
Офисные сотрудники чрезвычайно патриотичны :)
Совсем рядом располагается учебное помещение, в котором персонал отрабатывает моторику работы на конвейере. На стендах представлены двигатель, торпедо, шасси, подвеска. По словам собеседника, рабочие даже учатся закручивать болты на ощупь, тактильно различая один от другого.
Стенд каждого работника стандартизирован. У каждого человека инструменты должны располагаться в установленном порядке – именно в этом случае можно работать на ощупь, пользуясь только выученной моторикой.
Сразу хочу отсечь разговоры про превращение людей в роботов, поскольку каждые два часа работник меняется с коллегой и переходит к другой процедуре.
Специальные датчики следят за процессом сборки, индицируя красным сигналом светофора в том случае, если какой-либо из процессов не завершен, либо завершен с неправильными параметрами. Конвейерная линия, в случае красного сигнала, останавливается до устранения причин неисправности.
Супермаркет с запчастями, о котором я говорил чуть выше.
Автомобиль с собранным салоном проходит процедуру «Свадьба», в рамках которой кузов стыкуется с подвеской.
На заводе регламентировано время для обязательного отдыха, обеда и перерывов. Чувствуется западный стандарт.
Готовый автомобиль проверяет команда оценщиков, которые либо допускают машину дальше, либо находят незафиксированные ранее изъяны.
Прошедшие контроль автомобили загоняются к стенду, где сотрудники регулируют световой пучок и выравнивают развал и схождение колес.


Чтобы удостовериться в качестве сборки, готовые экземпляры тестируют на специальной площадке, после который обязательной является процедура мойки. Проблемные места, в которых выявили течь воды, свидетельствуют о браке производства, но, по словам сотрудников завода, эта мера является обязательной и отмене не подлежит, несмотря на отсутствие подобных ситуаций.

Экскурсия по автомобильному заводу немецкого концерна Volkswagen в Калуге окончена. Прессе отдают ключи от альтернативных комплектаций для того, чтобы экипажи попробовали как версии с механической коробкой передач, так и модификацию с шестиступенчатым автоматом.
Перед заменой лампочек снимаемых клему - с АКБ.
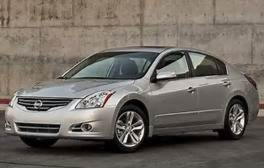
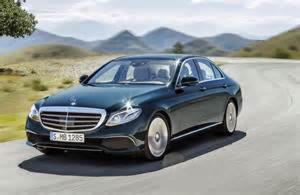
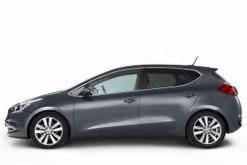
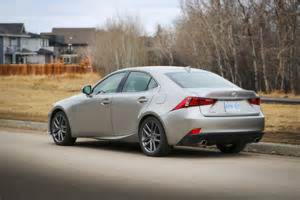
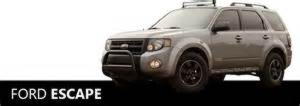

замена ламп ближнего света на VW Polo 6r Жанна | Автор темы: Валерия
в отличии от pololo sedan, где установлена 1 лампочка Н4 на ближний\дальний, в моей комплектации 2 лампочки Н1 и Н7 на ближний интересует сложность и методы замены из подкапотного пространства, т. к. в мануале указана замена со съемом блок-фары.
Виталий на шевроле лачетти тоже блок фары вынимать надо. там клипсы простые. главное не переусердствовать, чтобы не сломать, а то при торможении "глазки будут падать на бампер)))) "
Замена ламп в фаре Volkswagen Polo sedan - YouTube
Замена ламп в фаре Volkswagen Polo sedan. Volkswagen Auto Group ... Замена лампы ближнего или дальнего света, а так ...